In many parts of Africa, it’s common for young people learn a new job skill through an informal apprenticeship. But these apprenticeships are much different than the apprenticeships offered in places like the United States or Germany, where formal training at a trade school is often paired with the apprenticeship.
In Africa, apprentices often end up as little more than unpaid assistants working under a shade tree with old tools. Sometimes, the apprenticeship drags on for five years or more. Basic skills like taking accurate measurements are rarely taught.
Junior, a young man in Guinea-Bissau (West Africa), for example, had worked as an apprentice for a welder for many years, but he said the experience left him unprepared for real-world work. So he left his apprenticeship and enrolled in a nine-month welding course at a WAVS vocational school. He said this training helped fill in the major gaps missed in his apprenticeship.
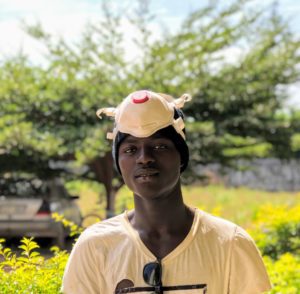
“I chose to come to the school and learn more about welding because I knew that if I want to do welding for my job I needed to improve my skills.”
— Junior, WAVS Welding Student
Here are 4 ways that vocational schools differ from apprenticeships in Africa
1. Vocational schools emphasize the basics
Apprentices rarely receive any formal instruction during their apprenticeship. Instead, they simply try to learn everything they can by watching the more experienced workers practice their trade. Usually, these “workshops” are little more than a work table under a shade tree or a tin roof. It’s common for the business to be run by a semi-skilled workshop owner and a handful of apprentices.
Since these semi-skilled workers never received formal training themselves, they lack basic skills like knowing how to take accurate measurements. They also haven’t been trained on how to effectively transfer knowledge to their apprentices. As a result, even after years working as an apprentice for years, many young people end up with only few skills and outdated techniques.
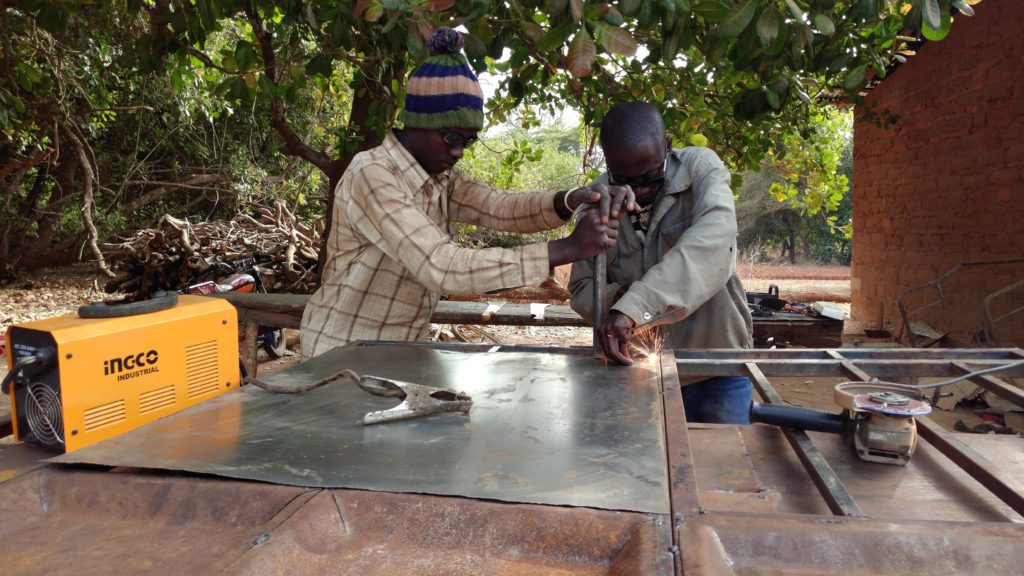
The typical apprentice in West Africa is usually an unpaid assistant working with rudimentary tools under a shade tree.
At WAVS vocational schools, welding courses start with the basics of welding. Since the majority of people in Guinea-Bissau only have 6 years of formal education, some simple math skills are taught at the beginning of the welding course. From there, the course teaches basic measurement skills to ensure their projects are built to specifications. This provides students with a strong foundation to build upon. By beginning with math and measurement skills that students may not be familiar with yet, this course becomes accessible to anyone — no matter their previous level of education.

WAVS welding courses begin with simple math skills to make sure students have a strong foundation.
2. Students are trained to be able to complete a project by themself, rather than just help as an assistant
Often, workshop owners don’t actually want their apprentices to learn the skills that would allow them to start their own workshop. They are worried that their apprentices might become their competitors. They also don’t want to lose their free assistants.
At WAVS vocational schools, students are taught every aspect of a trade. This includes learning about different types of welding techniques, welding safety, and machining work. Graduates are prepared to problem-solve for themselves and take on projects single-handedly. Many of them, including graduates like João, are able to earn a reliable income themselves and provide for their families.
Graduates from WAVS vocational schools are able to earn money for themselves and their families.
3. Students receive their own tools after graduating
Apprentices often only get to work with old, outdated tools. WAVS graduates get to purchase welding supplies at subsidized prices thanks to the New Entrepreneurs Program. These welding kits allow for graduates like Nilton to open up their own workshops and start working immediately.

The New Entrepreneur Program kits provide graduates with tools at discounted prices.
Even with the subsidized prices, getting started can be difficult. That’s why students are also taught how to build their own basic tools out of common items. This allows them to save up to purchase a starter tool kit, or get started on simple enough projects until they earn enough for one.
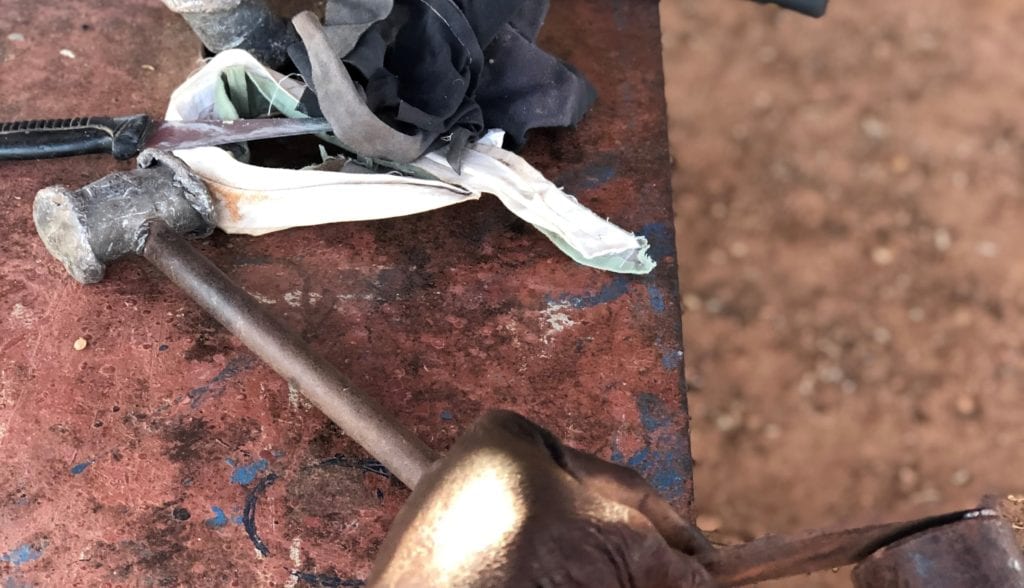
WAVS students are taught how to make their own tools out of common household items.
4. Students get hands-on experience working on big projects
Apprentices working for road-side workshops usually are limited to auto body work, repairing bikes, or fabricating simple doors and windows. Rarely do they get experience working on large-scale projects. But at WAVS vocational schools, the staff and students team up to take on projects like installing school roofs or security gates. This experience makes WAVS graduates desirable hires.
There’s another benefit as well: the local community has a place to go to hire quality workers. WAVS instructors take on community projects that generate revenue for the school while also giving the students real-world work experience (interested in what a day in the life of a welding student looks like? Click here).
Welding students installing a roof on a local agricultural co-op WAVS students built and installed a security gate for a local bank
5. WAVS graduates are raising up the next generation of skilled trade workers in their communities
Several WAVS graduates are part of a new generation of workers who are running apprenticeships the right way. Ciro and Cirilo are two examples. Both of these WAVS graduates run their own workshops with several apprentices. They also help pay for their apprentices to complete the WAVS welding program. The training the apprentices learn at the WAVS vocational schools, combined with their experience working as apprentices, prepares them for real-world work.
Ciro and Cirilo are both WAVS graduates who now send their apprentices to WAVS vocational schools.
Junior was able to afford tuition at the WAVS vocational school thanks to One Student members who help cover most of the cost of his training. Today, you can join this community of monthly donors and give more young people like Junior the same opportunity, one student at a time.